
Scale build-up is one of the major challenges in water processing systems, not only reducing pipe and equipment effectiveness but also slowing down water flow. Over time scale and corrosion may also lead to pipe walls weakening and then leakages.
Scale can significantly impact the bottom line of building operations. Typically, for a 100,000m2 building, average annual HVAC (Heating, Ventilation and Cooling) operation average expenditure is already over USD650,000/year (USD470,000 for energy, USD130,000 for water & USD50,000 for chemicals), but scale in the system will add 10-25% to the energy bill (for example, 3mm – or 1/8” – of scale adds some 25% extra energy)!
One common solution is using chemicals, which removes about 90% of scale build-up. However, on top of the thousands of dollars in chemicals cost, this requires frequent chiller cleaning which also reduces equipment life expectancy – again meaning higher operational and capital costs for building managers.
So, what could be a better solution?
ScaleBuster and EnviroTower, two innovations that help building manager tackle scale corrosion while saving water, energy, chemical use and costs, and also eliminate the chillers clean-ups that reduce life span of these expensive pieces of equipment.
ScaleBuster & EnviroTower – how do they work?
ScaleBuster®
ScaleBuster is a water conditioning technology that provides control of scale and corrosion in various water process systems. Operating everywhere from power plants on an industrial level to homeowners on a domestic level, the technology can completely replace traditional chemical treatment of certain water systems.
The ScaleBuster works by making the calcium and magnesium in the system precipitate into suspension. When these particles reach the hot parts of the system, the tendency to adhere to surfaces is dramatically reduced, thereby protecting equipment from potential limestone damage with relatively fast return on investment.
Since 1990, this device has already been applied into over 300,000 applications by distributors across Europe, North, Central & South America, the Middle East and Asia.
EnviroTower®
Designed around the ScaleBuster, EnviroTower is a cooling tower water treatment technology. It works by precipitating the hardness (typically, Ca++ and Mg++ ions) in the cooling water, causing those ions to build clusters which grow larger as the water is recirculating through the ScaleBuster conditioner, until they are removed from the water by the cyclonic separation or filtration process.
In total, it can eliminate 98-99% of scale, comparing to only 90% by chemical treatment. This can help building managers save resource use in 3 ways (bottom line scenario):
- Energy – 10-25% cut: The EnviroTower shows superior protection against scaling and fouling build-up which reduces chiller efficiency by up to 25% and more in some cases. This can potentially increase to 15% of energy saved as more head pressure in the chillers is needed when the system scales up.
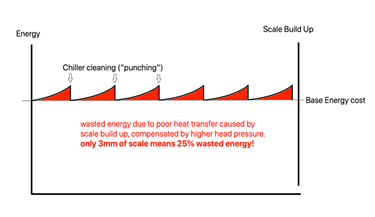
- Water – 10-15% cut: When a cooling tower evaporates water to lose heat, the remaining mineral buildup will cause corrosion and damage the equipment. That’s why a blow-down, meaning water is being drained to remove minerals, is needed regularly. However, blow-down (or “bleed”) in wrong timings and frequencies might lead to water wastage or corrosion.The EnviroTower allows cycling up, or in simpler words, it uses the water more times through the towers before the blow-down. By controlling the blow-down according to water conductivity, the system can save water and avoid mineral buildup at the same time.
- Chemicals – 85-97% cut: The EnviroTower uses less chemicals by “shocking” the water only once per day (with both biocide as Bromine and Azole, which protects the copper in the chillers). What’s more, water discharged from the cooling system is so low on chemicals that can be re-used for irrigation or other purposes.
- Maintenance and chiller cleaning (“punching”) cut: With EnviroTower the annual chiller cleaning can be avoided, saving both the immediate cost (OpEx or Operational Expenditure) and the shortening of the life span of the chillers (as mechanical scale removal also removes copper from the chiller tubes, not allowing for the theoretical life span it was designed for) postponing the need for investing in new chillers (which is CapEx or Capital Expenditure).
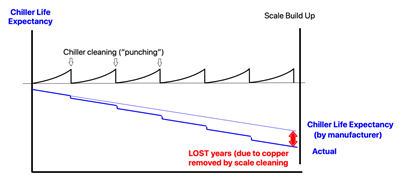
Cost saving for building managers
Overall, EnviroTower can add 15-25% to equipment life expectancy and save 10-20% on operating costs (with typical ROI of 12-36 months) as shown below:
![]() |
![]() |
Image 3: Actual savings calculated by a US Medical Center in 2018 following operation of 3 EnviroTower systems for years, the first installed back in 2008 and 2 others had followed in 2015
To describe the cost saving more vividly, the pie on the left shows potential operational savings (or OpEx) for a cooling system after installing an EnviroTower solution. The pie on the right added the significant Capital Expenditure (CapEx) saving by the lack of need to replace a chiller earlier than planned, based on the following: on a USD2mn chiller designed for 20 years, it can be looked at as USD100,000 per year (before getting into amortisation calculations, interest rates and so forth). Every chiller cleaning reduces life span, so frequent cleaning might reduce up to 6-7 years from the expected 20 years which are equal to $600-700,000!
For more on these two innovations, click here.