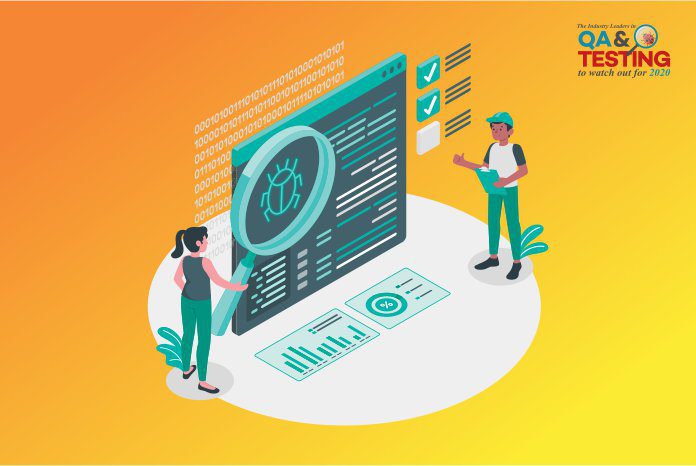
Quality management marks the degree of excellence of a service or product as a confirmation that it is reliable, durable, and cost efficient. When a customer purchases a product, it is a prerequisite to ensure that the customer receives a value for money experience. Every customer appreciates quality which is an important element in gaining the loyalty of the customer and a loyal customer is an asset to a successful business.
Quality assurance is a long process that involves many administrational procedures to eliminate the errors. Hence, quality management is an innovative tool that is created to simplify the complexities. Systematic measurement, monitoring the process, and gathering constructive feedback confers error prevention. Let us understand the introduction, importance, and practice of quality assurance.
The Concept of Quality Assurance
Many decades ago, during the first world war there was a growing demand in the manufacturing industry which introduced the need for mass production. This increase in production gave birth to negligence with reference to quality. The increase in demand called for a rapid hire of workers to deliver the requirement in time. As a result, quality was compromised. There were many business leaders who recognized that there has been a subsequent dip in quality with the increase in production. Henry Ford was among the few who came up with the innovative concept of standardizing the manufacturing of a product as per set guidelines and at the same time ensuring the quality of it by placing managers or supervisors for the inspection process.
Following this thought, quality management kept developing with the introduction of statistical process control. Recognizing the importance of quality, it started becoming a mandatory practice for every organization to adapt a strict quality check to maintain the profit ratio. As a result, quality became a crucial part of every business and with the rise in technology, quality management too transformed from obsolete techniques to modernized digital standards.
The Importance and Widespread
When we come across the term “quality check” we are assured that the product has been tried and tested and has undergone the error elimination process which confirms it is ready for use. There are numerous measures taken to produce a hundred percent quality product, however despite the efforts there is always scope for human errors. Subsequently, many organizations started creating quality management tools with the help of technology and artificial intelligence. Digitization annihilates errors to a great extent and optimizes the process of quality assurance. These tools are created as per standard guidelines to meet the quality needs of the company.
ISO 17025 is an international standard that calibrates the competence test of a product which includes 15 management and 10 technical requirements. ISO 9001 is a quality management system that regulates the quality check of a product according to set standards. These standardized marks were introduced once the importance of quality was fathomed. Today, ISO is a worldwide mark of excellence to measure quality.
Quality assurance exists in every field today. Medical, manufacturing, software, aerospace, and every field of business that depends on the feedback of satisfied customers. Hence, maintaining accurate and up to the mark quality is not only a standard but is the right of every customer that businesses must deliver.